HolzBAU25 – Work in Progress
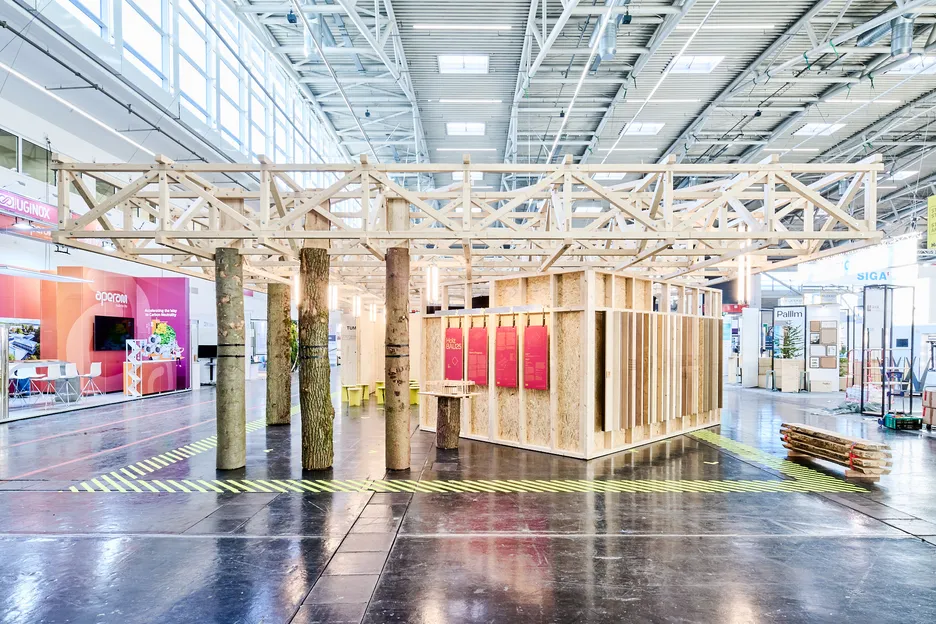
In order to inform the general public about the climate protection potential of building with wood at the BAU25 trade fair, the Bavarian State Ministry of Food, Agriculture, Forestry and Tourism, together with the TUM.wood Group, initiated the “HolzBAU25” design-build project at the Technical University of Munich (TUM). In the summer semester of 2024, the Chair of Architecture and Timber Construction at TUM focused on the planning and realization of the exhibition pavilion made of wood. The aim of the project was to vividly convey the value chain “From tree to house”. Thanks to a flexible construction with reversible connections, the pavilion can be reused and repurposed in different contexts in the future.
In spring 2024, 18 architecture students began developing ideas for the timber pavilion at BAU25 in Munich. They were supported by staff from the Chair of Architecture and Timber Construction. From various approaches, three designs were worked on in depth in teams before a project was finally selected for realization at the end of the semester.
Different elements take on the vertical load transfer and divide the space below into zones with varying qualities.
Thanks to the non-directional roof construction, the arrangement of the vertical load-bearing components can be flexibly adapted to changing usage requirements.This allows new spatial constellations to be created without having to make any changes to the supporting structure itself.
Last summer, the students worked out the design in detail, coordinated it and prefabricated it in the 1:1 workshop at TUM over the following months. After successful test assembly, the pavilion was dismantled into its individual elements, loaded and stored.The process was documented on film, the video can be seen in the pavilion.
The HolzBAU25 pavilion demonstrates almost the entire range of possible applications and capabilities of wood and wood-based materials.
The truss girders of the roof structure are made of 8 x 8 cm solid structural timber bars.
They form a spatial supporting structure that cantilevers in all directions. No metal fasteners were used; instead, the bars are reversibly connected using laminated veneer lumber panels.
The vertical load-bearing and bracing elements are also curated from different wood products in an exemplary manner.Individual supports are made from raw beech, oak and spruce tree trunks. In contrast, there is a support made of laminated beech veneer lumber (BauBuche), a highly processed and high-performance construction element. Reused cross-laminated timber is used as a wall cross and timber panel construction elements are used as two-dimensional load-bearing elements to create the space of the inner volume.
A three-dimensional truss model was created for the roof structure, from which the internal forces for the further dimensioning of the components and connections were derived. The almost isotropic material properties of the cross-glued laminated veneer lumber panels allow them to be used as slotted plate-like connecting elements. These panels are coupled to the truss members at the junctions using reversible bolt connections.
The various columns and walls form the supports for the roof structure, with the latter also ensuring the spatial bracing of the pavilion. Simple fork bearings are used to transfer any horizontal forces from the roof.
“Work in Progress” - The unfinished aesthetic of building on and reusing embodies the dynamic processes of a changing construction sector. It stands for the transition to a sustainable, resource-efficient building culture.
Project participants
Patronage
Bavarian State Ministry of Food, Agriculture, Forestry and Tourism
TUM.wood - Network for Research and Teaching
Project participants
Architecture: Technical University of Munich
Chair of Architecture and Timber Construction, Prof. Stephan Birk
Project management: Jonas Faber, Jonas Wolf
TUM.wood Group: represented by Dr. Sandra Schuster
Project work by students of the TUM:
Ameli Dammann, Antonius Viehmann, Augustė Gasperaitytė, Carlos Antonio Meza Colin, Emiel Depoortere, Isil Alimoglu, Jakob Matthaei, Kaisa Heidsve, Lena Marie Mayer, Loenard Jasper Lowen, Lovro Urbancic, Lukas Maier, Mohammad Beiglari Gholdareh, Pauline Geiger, Sara Font I Jiménez, Senne De Ridder, Tomas De Landsheer, Yuejiao Xie (all involved in the design and implementation planning); Barbara-Rosa Sievi, Chistoph Pöllmann, Domenico Introcaso, Dorsa Harandian, Emiel Depoortere, Florian Schön, Florian Rathey, Florian Schönwetter, Jana Lohr, Jeffry Nwabuodafi, Johanna Simons, Kai Sun, Lena Meyer, Lilli Dolderer, Lilly Yousefina, Livia Gößwein, Manuela Schiffner, Max Pauli, Maximilian Kroth, Milla Kaschub, Nadine Lehmann, Paula Diederichs, Sophia Lamparter, Yuejiao Xie (all involved in prefabrication); Anna Friedel Schulz, Bomi Som, Carina Lindenberg, Christoph Pöllmann, Daniel Aschenbrenner, Fabian Bartl, Florian Leussing, Gina Weiß, Guneş Yazar, Henry Höcherl, Jooyoung Lee, Justus Raufhake, Lukas Litterst, Lukas Binder, Maja Weidner, Pedro Ruwer, Philip Swoboda, Goncalo Portal, Rouven Tedoskino; Sophia Freiin von Wangenheim, Teodora Bordas (all involved in construction and dismantling)
Prefabrication: TUM Design Factory, Nora Singer and Sandra Kahl
Structural design: Shortlist GmbH, Wasserburg/ Munich
Graphics: Digital Loop, Munich
Timber construction (joinery, transportation):Gumpp & Maier GmbH, Binswangen
Laminated veneer lumber beech: Pollmeier Massivholz GmbH, Creuzburg
Cross laminated timber (ReUse): Rubner Holzbau GmBH, Brixen
Wall mural wood materials: Mannich-Planungen, Marktoberdorf
Curtain rail: Breidenbach Metallbau GmbH, Peiting
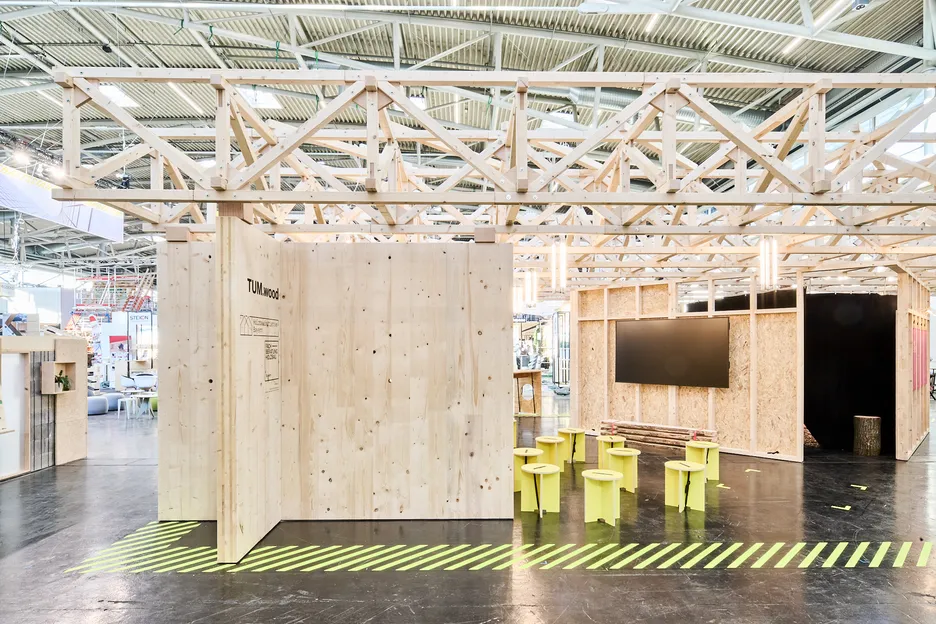
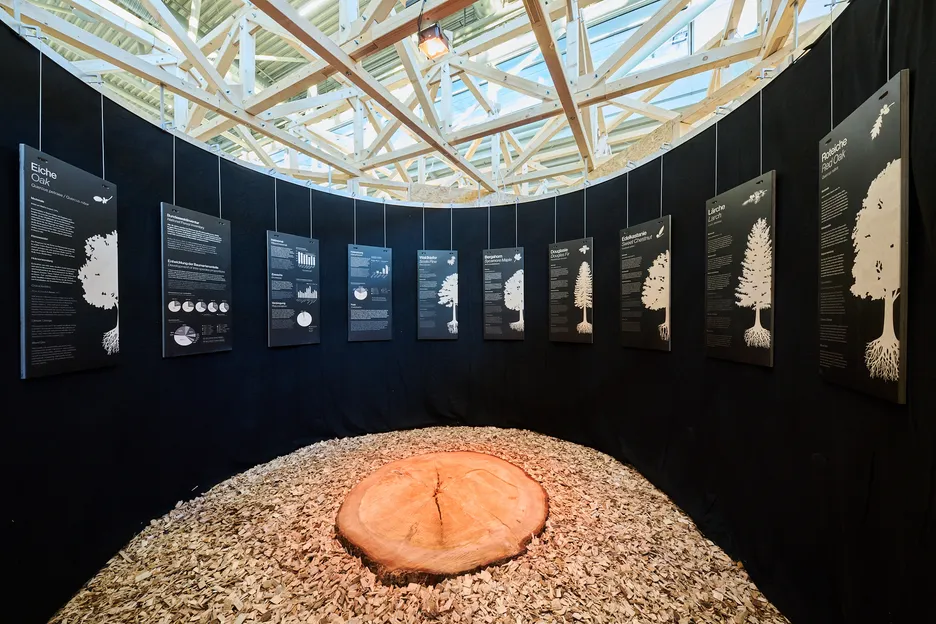

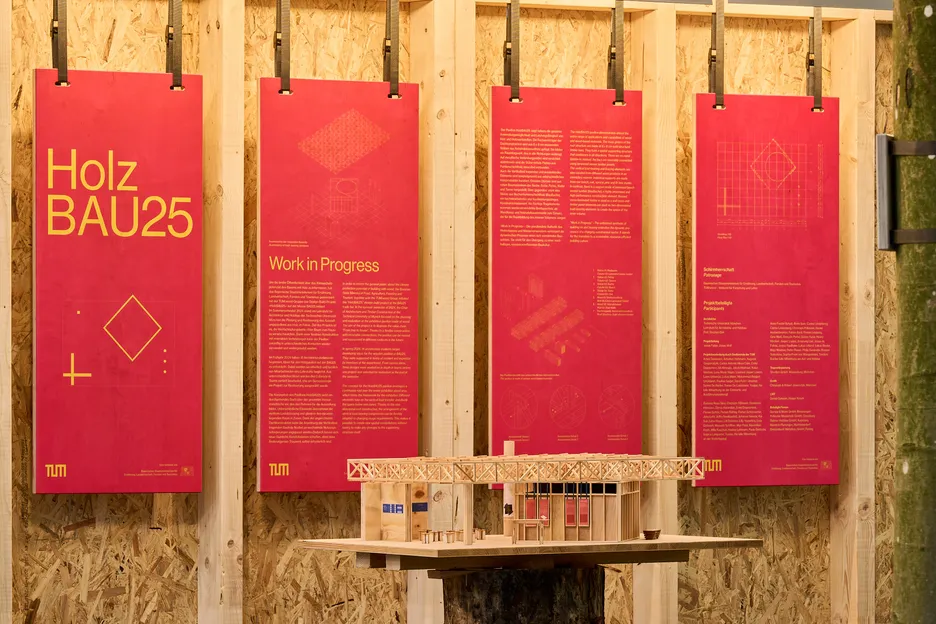
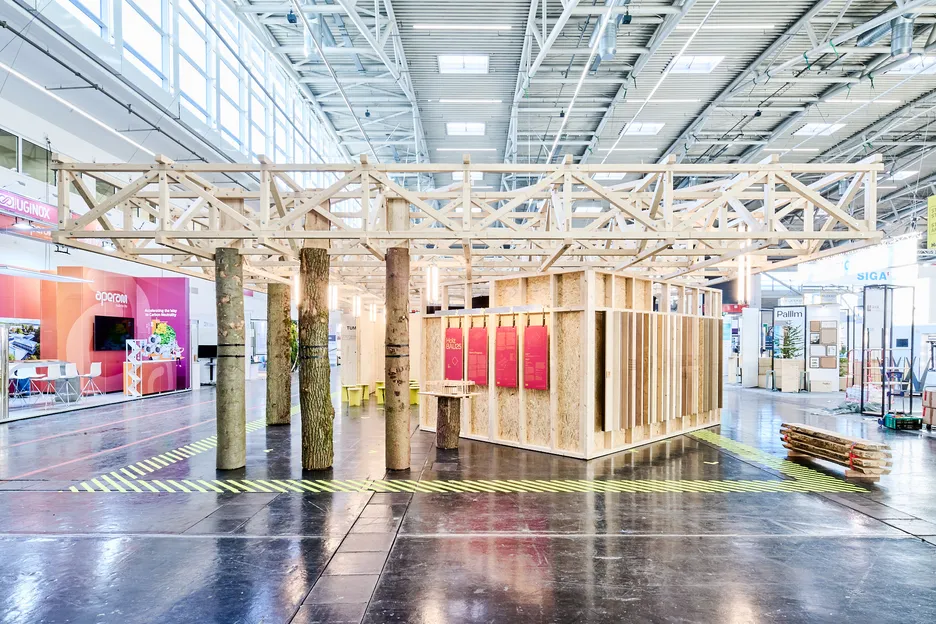
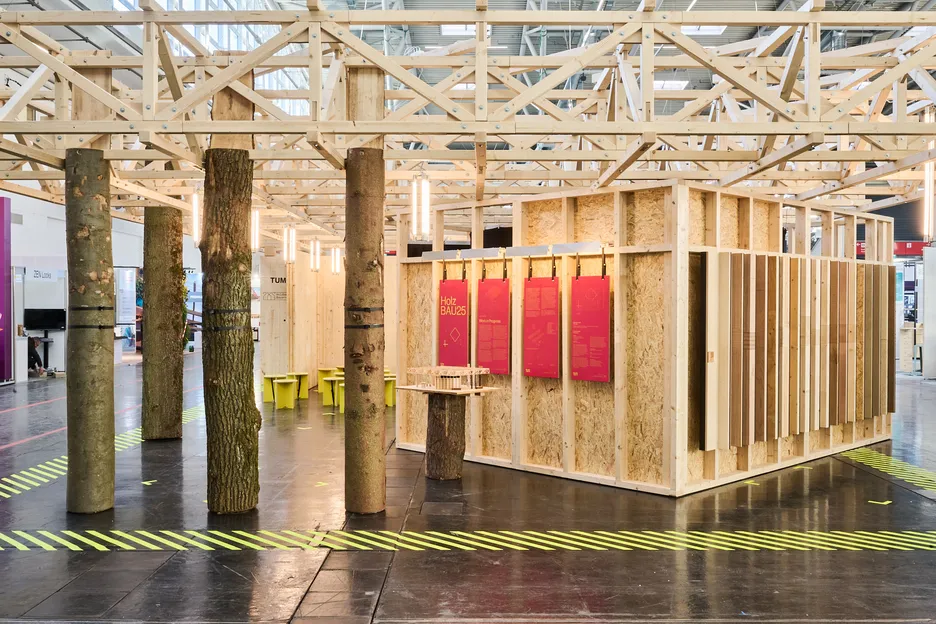
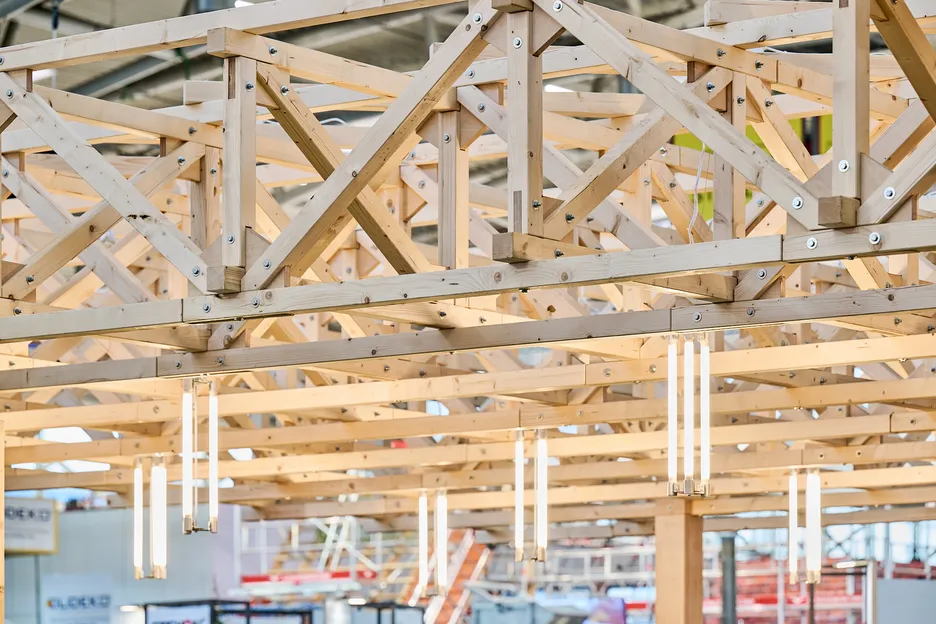
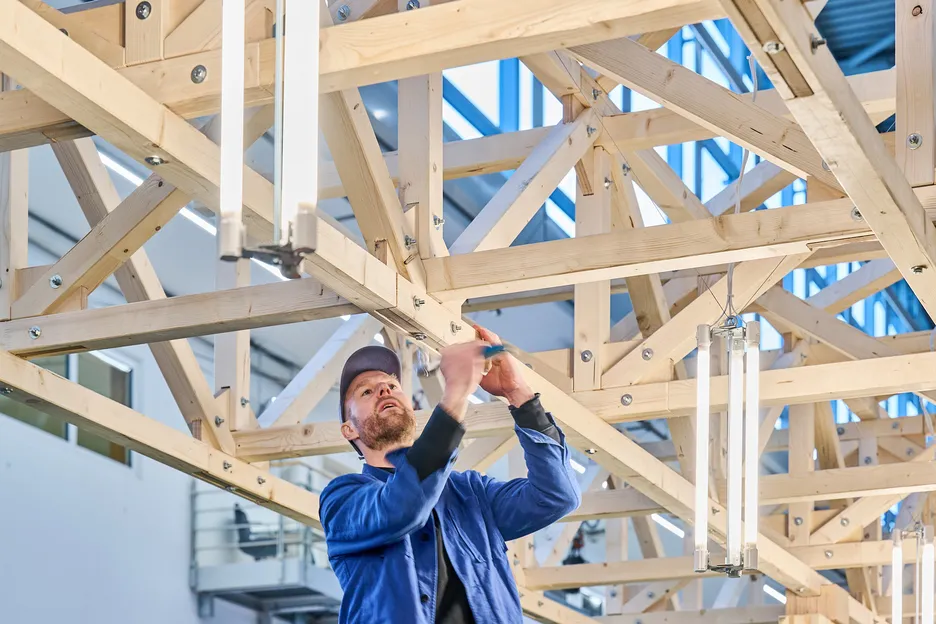
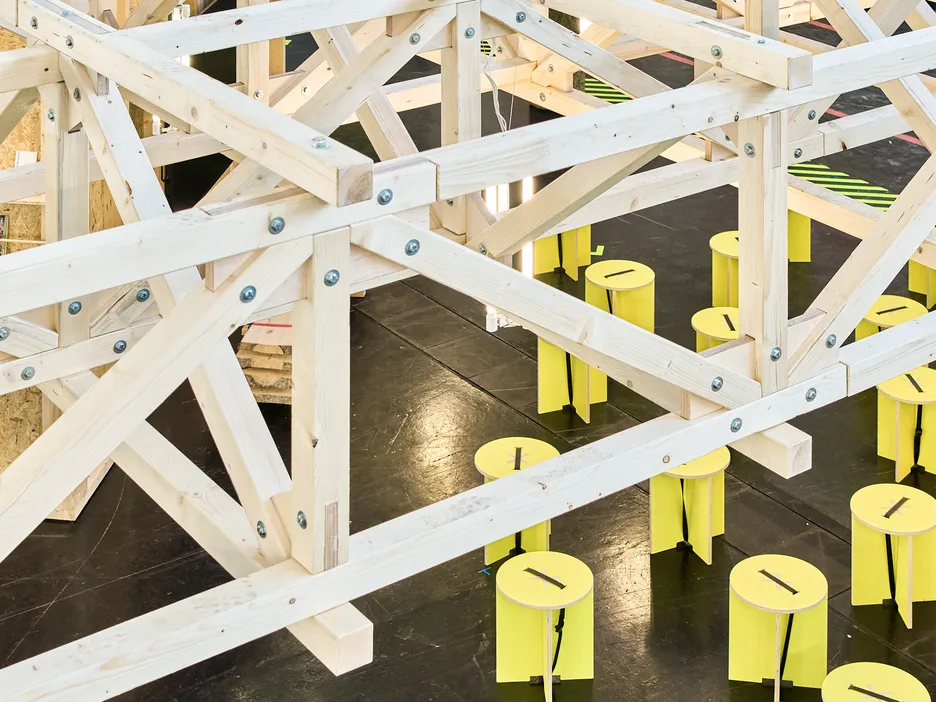
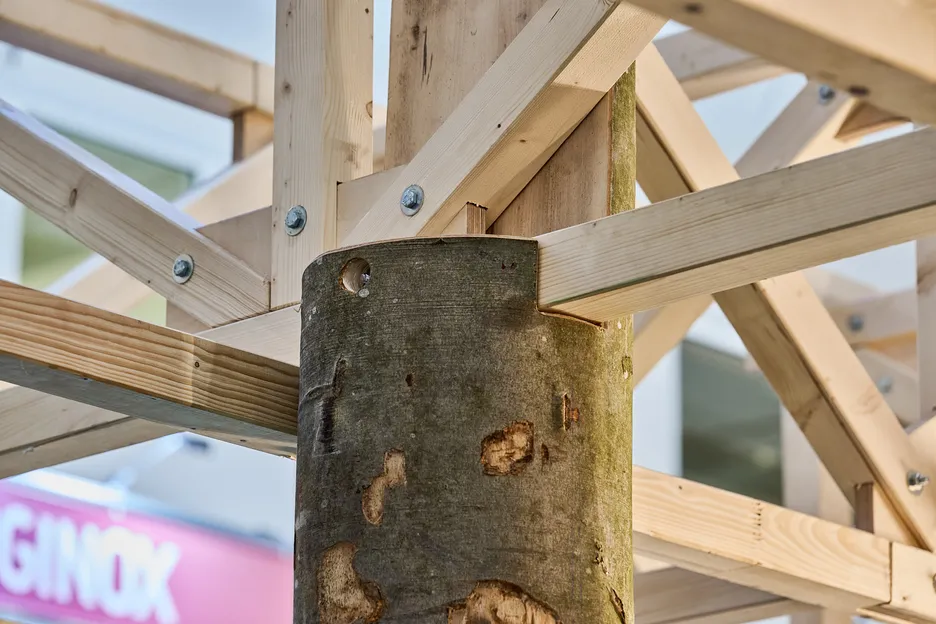
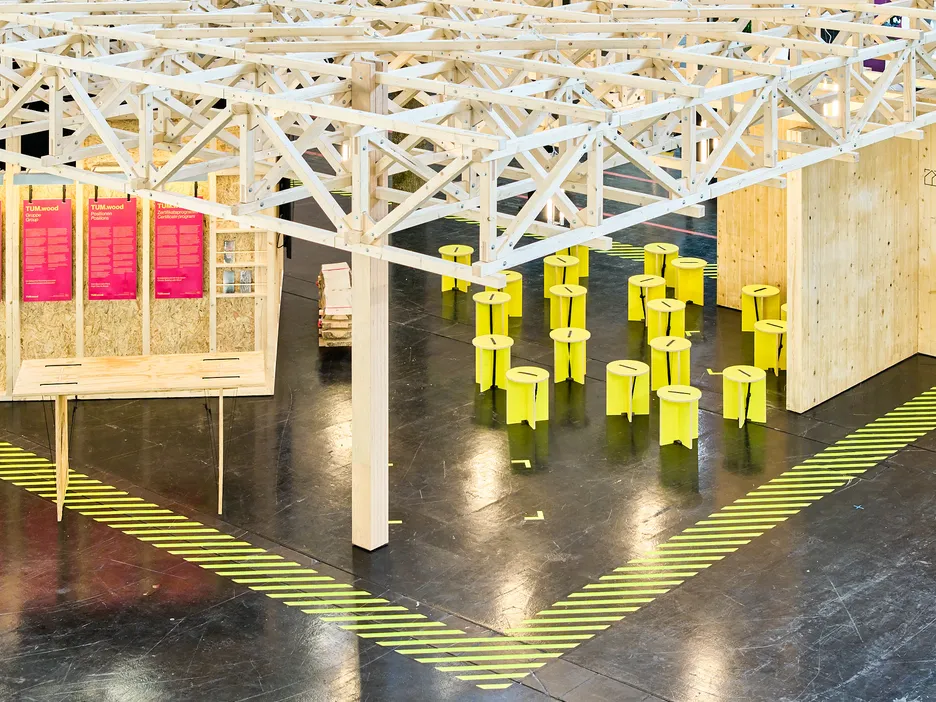
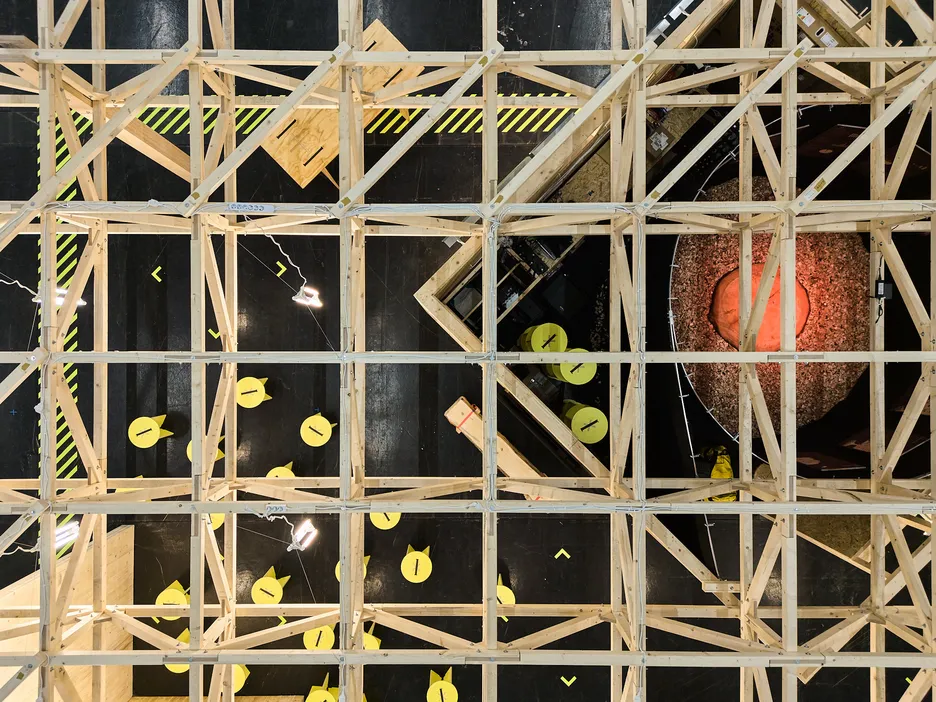
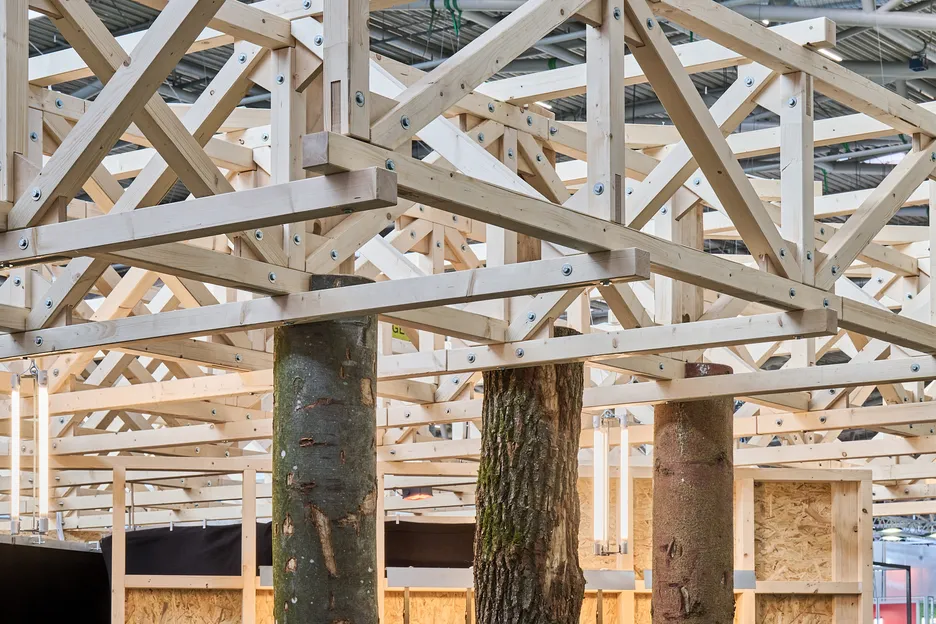
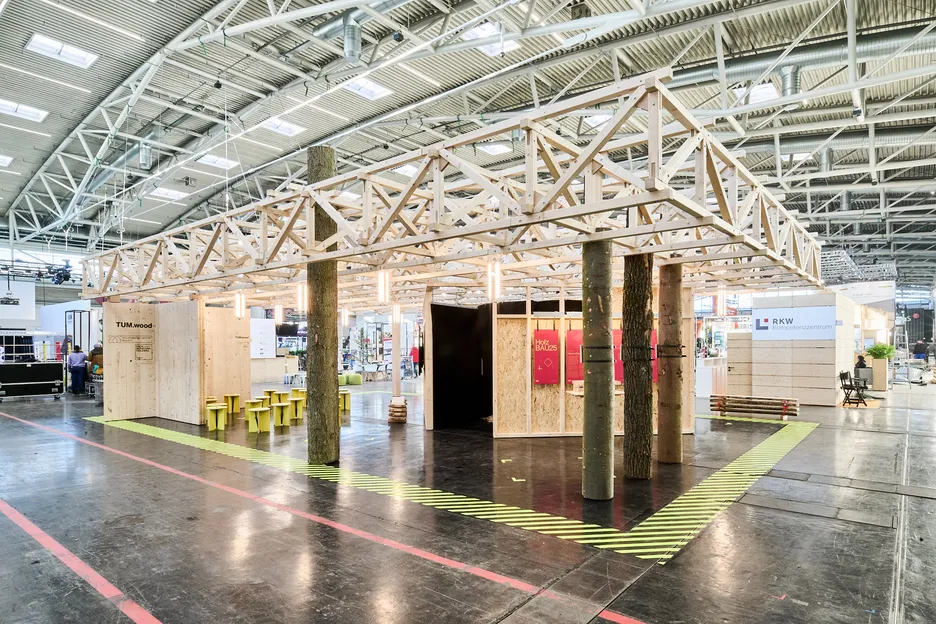
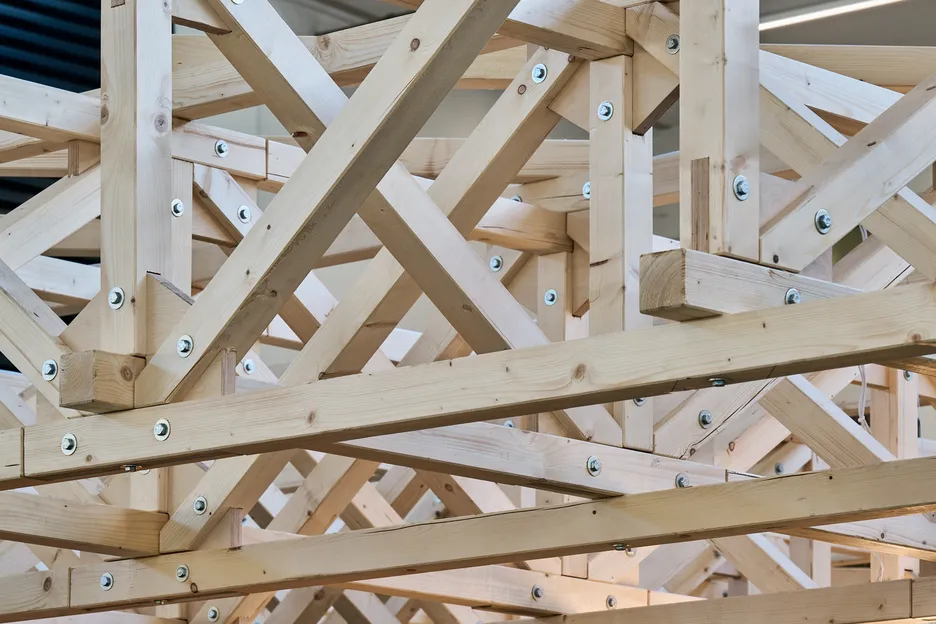
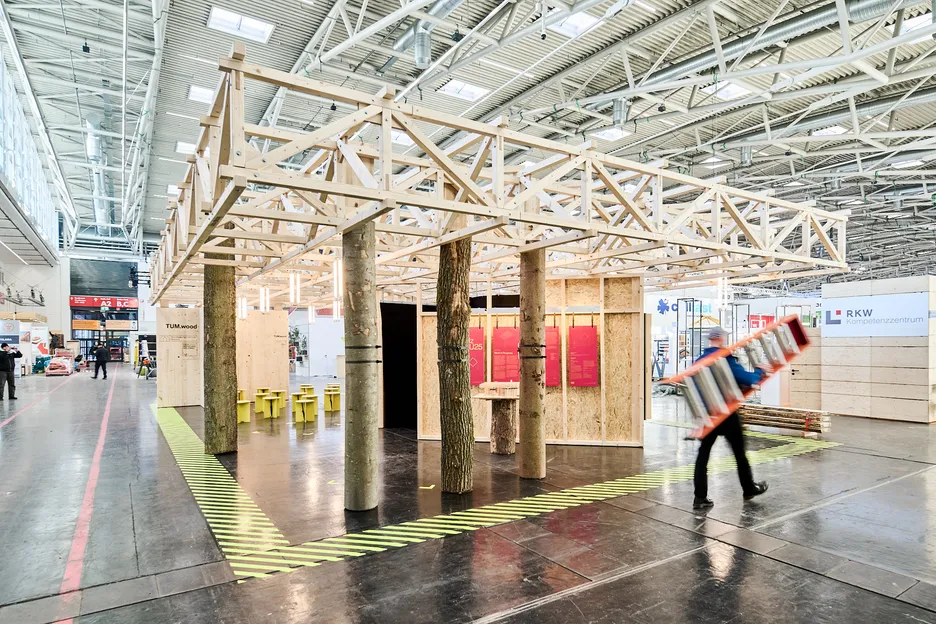
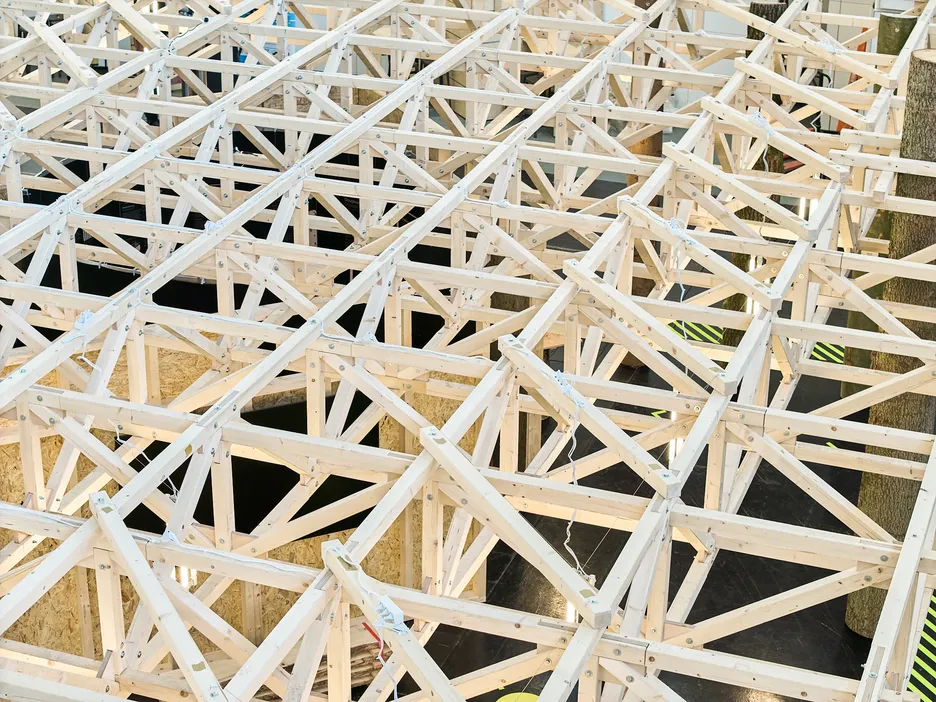
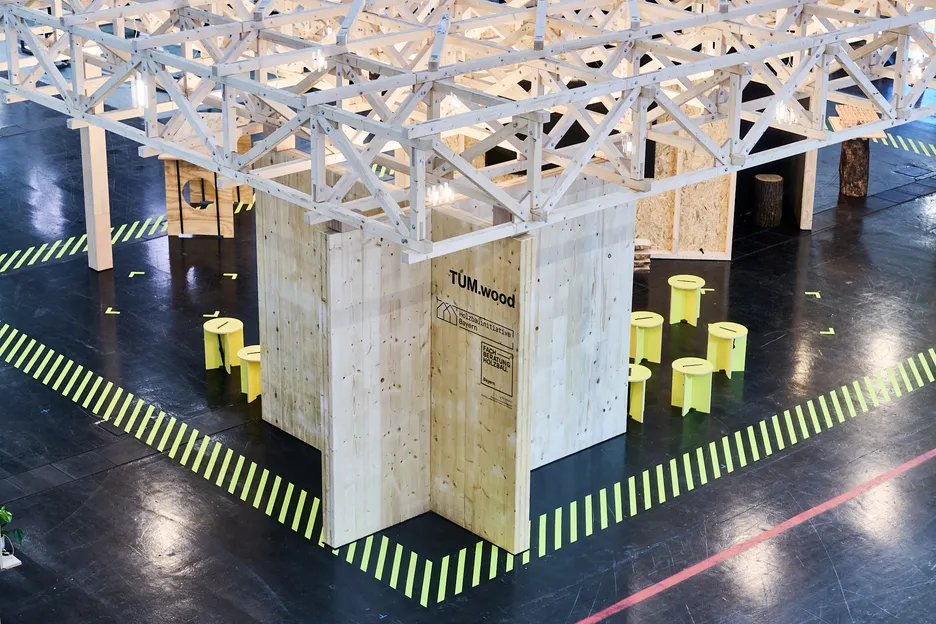
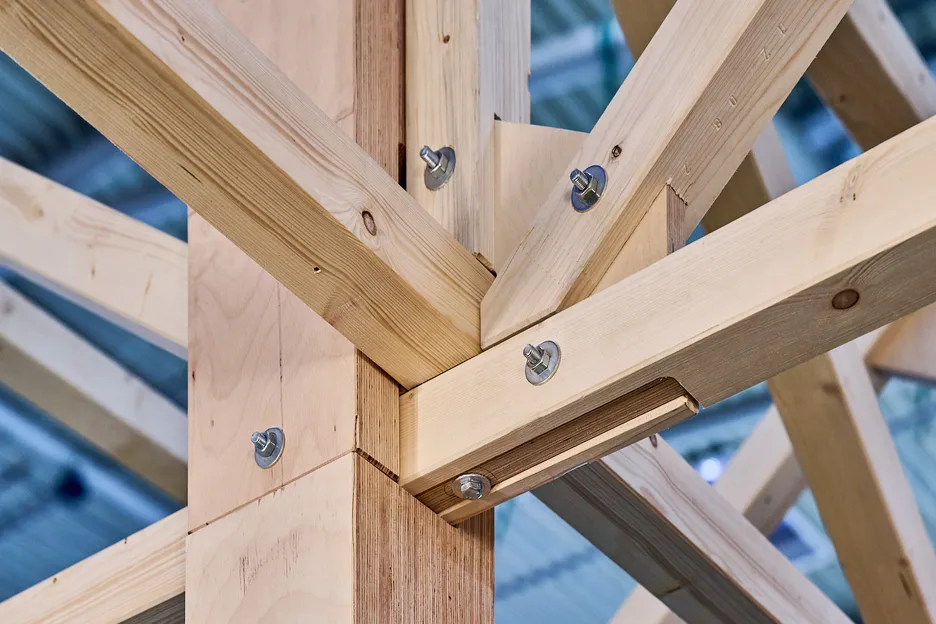
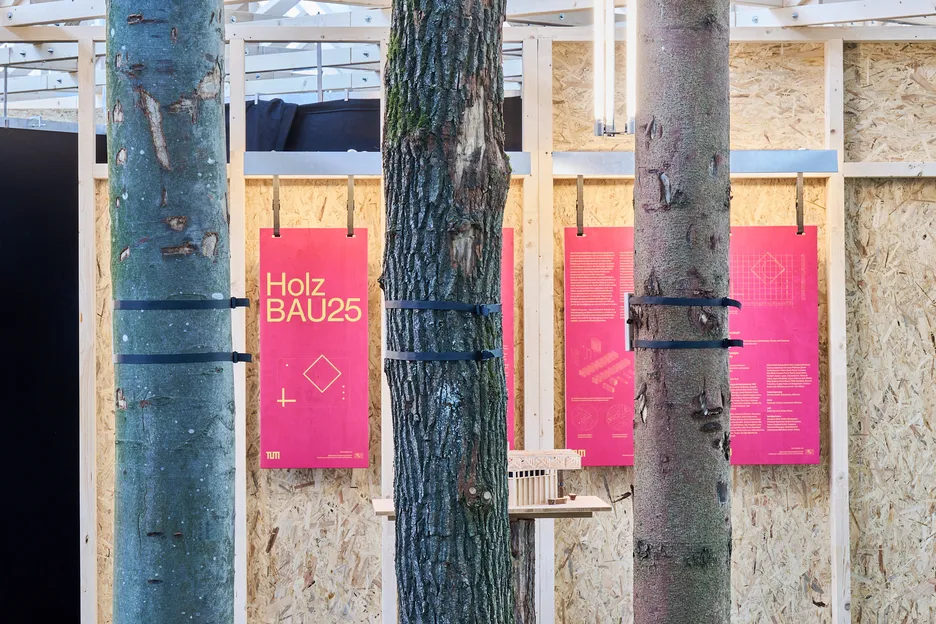